The DUKW made safe at sea
Setting the record straight on DUKWs. The media’s negative portrayal doesn’t float.
From time to time there are media reports critical of “duck boats” – as the media often reports them. In truth, few of the vehicles being harshly criticized are true DUKWs, and most assuredly, any that are true GMC DUKWs have been extensively modified. The DUKW arguably had more engineering know-how devoted to it than any other vehicle in the U.S. Army’s WWII arsenal. The record should be set straight regarding the vehicle’s design and safety.
The DUKW pedigree
The amphibious truck was the result of work of a government agency outside of the War Department, the National Defense Research Committee, or NDRC. The NDRC was the brainchild of Vannevar Bush. Bush, born March 11, 1890 in Everett, Mas., received his Ph.D. in engineering from the Massachusetts Institute of Technology (MIT) in 1916. While Bush was an accomplished engineer and inventor, perhaps more importantly, he was a notably competent science administrator. In 1932 he became vice president of MIT and dean of the MIT School of Engineering, and in 1938, president of the Carnegie Institution of Washington. Also in 1938, he was appointed to the National Committee of Aeronautics (NACA), forerunner of today’s NASA, and following the retirement of Joseph Ames in October 1939, Bush became NACA chairman.
Seeing the signs that the United States would soon be mobilizing for war, and concerned about a disconnect between the nation’s military and rapidly advancing science, Bush formulated a plan to create a committee remedy this condition. When Hitler invaded Poland, the matter became somewhat more urgent, and Bush managed to arrange for a June 12, 1940 meeting with President Roosevelt. The brief meeting was positive, with Roosevelt approving his proposal.
This approval was formalized a on June 27, with the newly formed National Defense Research Committee being placed under the auspices of the Council of National Defense, which had been created in 1916 “for the co-ordination of industries and resources for the national security and welfare.”
The eight people to make up the committee included two who were appointed by virtue of their positions as president of the National Academy of Sciences and Commissioner of Patents respectively, four who were appointed without reference to other offices, and two who were selected by the Secretary of War and the Secretary of the Navy respectively. All served without compensation.
As specified in a 15 June letter, Bush chaired the committee.
With a broad task ahead of them, it was apparent that the work of this committee had to be broken into various subgroups, and as it was the intent of the NDRC to coordinate the nation’s entire scientific community in regard to defense, five divisions were created.
Division C, Communications and Transportation, was to be chaired by F. B. Jewett. This division was later renamed Division 12.
A year and a day after the establishment of the NDRC, the structure of the organization changed. Executive Order 8807 signed on June 28, 1941, established the Office of Scientific Research and Development (OSRD). Notable was the addition of “and Development” in this organization’s name.
While the NDRC was originally placed under the Council for National Defense, the OSRD was put within the purview of the Office of Emergency Management of the Executive Office of the President. The director of the OSRD would be appointed by, and report directly to, the president of the United States. Executive Order 8807 specifically moved the NDRC to the auspices of OSRD.
President Roosevelt named Vannevar Bush as director of Office of Scientific Research and Development. Bush, feeling he could not direct both OSRD and NDRC, appointed J. B. Conant as chairman of NDRC.
One interesting aspect of both the NDRC and OSRD operations was the premise that research itself should be non-profit, whether conducted by an institution or university, or by a commercial enterprise. The contracts used by NDRC/OSRD were therefore structured so that those contracted would neither gain nor lose financially for the work contracted.
The Amphibian idea is Born
It was to Division C that the Quartermaster Corps turned for help in designing an amphibious vehicle on May 7, 1941. This request would have come to the attention of 58-year-old Hartley Rowe, chairman of the Transportation section. Rowe maintained his office at 1 Federal Street, Boston, in the headquarters of United Fruit Company. Rowe had become the company’s chief engineer 15 years earlier. With an electrical engineering degree from Purdue University, Rowe had served as resident engineer, Building Division, of the Panama Canal until August 1919. Equipped with theoretical expertise and years of on-the-job experience, Rowe not only had a clear grasp of engineering in general, but also a feel for administering large-scale and complex engineering projects. Fortuitously, Rowe’s experiences also provided insightful knowledge into the difficulties of moving cargo, be it bananas or munitions, from ship to shore.
Rowe assigned the amphibian project to his 40-year-old executive officer, Palmer Cosslett Putnam. A holder of a degree in geology from the prestigious MIT, Putnam was the son of George H. Putnam, president of G. P. Putnam’s Sons Publishing Company. Palmer Putnam took over as president of the publishing company upon his father’s death in 1924, but then retired from that post in 1932.
Intrigued by the high winds – and the high cost of electricity – on Cape Cod in 1934, Putnam envisioned a large-scale wind generator system as a cost-effective alternative. He crafted a preliminary design with cost estimates, and in 1937 sought the advice of the dean of Engineering at MIT. The dean, who was impressed by Putnam’s work, was Vannevar Bush. Ultimately, Putnam did erect a large experimental wind generation plant in 1941, and until the 1980s, Putnam’s 1.25-megawatt wind turbine was the largest in the world. Technically successful – if not economically profitable – the turbine led NASA in 1974 to recognize Palmer, saying “Whatever has been accomplished in the U.S. in an effort to develop the wind as an important source of power can be credited largely to the imagination and talents of one man – Palmer C. Putnam.”
Putnam, like many of his family and contemporaries along the seaboard, made a hobby of sailing. Palmer C. Putnam was a founding member of the Stone Horse Yacht Club, Harwichport, Mass., in 1933.
He was undoubtedly familiar then with two brothers who were the sensation of the international sailing scene, Olin and Roderick Stephens, Jr. The sons of a successful coal dealer, both had a strong interest in sailing and vessel design. Olin, along with yacht broker Drake Sparkman formed the design firm of Sparkman & Stephens on Nov. 11, 1929.
In 1931, a yacht they designed for their father, and crewed by the family and friends, entered the Transatlantic Race from New York to Plymouth, England. That vessel, the Dorade, arrived in Plymouth in 16 days and 55 minutes – besting the competition by two days (almost four days on corrected time). Roderick Jr. (Rod) joined Sparkman & Stephens as a designer in 1933, and won the Transatlantic Race in 1935. Olin would go on to be the original designer of six successful 12-meter defenders of America’s Cup from 1958 through 1980.
Joining the payroll at Sparkman & Stephens in 1942 was British immigrant Dennis Puleston, a much-acclaimed seaman and adventurer. Until his U.S. citizenship was conferred, Dennis was unable to work on classified projects, a restriction that was lifted when he became a citizen early in 1942. Once this status was attained, he immersed himself in work that included a project of the OSRD concerning amphibian vehicles. Puleston was so deeply involved with this project that after WWII he was tasked first with writing the detailed technical report of all the wartime activities of Division 12, and later became director of the group that compiled all 72 volumes that chronicle the wartime work of the OSRD, occupying an entire floor of the Empire State Building to do this.
This group of men were first tasked with a project known as the QMC-4, which became the Ford GPA. As Palmer C. Putnam wrote in a memo regarding the outset of the QMC-4 project “…whereas there are several dozen people in the country who could whittle out a passable battleship, there was nobody who could whittle out a passable amphibian.”
The creation of the GPA had resolved many of the unknowns. The Sparkman & Stephens hull design had proven viable, Clarence Kramer of Ford had refined the hull form so that it could be produced in an automobile assembly plant, and effective water seals for the powertrain had been developed.
There remained, however, the problem of transporting large quantities of men and equipment to shore. The GPA was never intended to address this – it was an amphibious scout car. A large amphibian would be required to quickly move tons of supplies and thousands of men ashore without the use of proper dock facilities, which no doubt would be savaged by both defending and attacking forces during a war. Hartley Rowe had broached this subject with Vannevar Bush prior to Pearl Harbor, but the Army initially exhibited a notable lack of interest in such a vehicle.
This situation changed, however, on March 24, 1942, following the successful first tests of the ¼-ton amphibian. Initially, the vehicle that became the DUKW was conceived as a ferry for tanks, but the requirement would evolve. Initially, the NDRC approached Ford, owing to their experience with the GPA. When Ford declined, on April 16, Putnam, along with Rod Stephens, brought the problem to General Motors Yellow Truck and Coach (GMC). Initially, several in the Army objected to the project, but the NDRC persevered, and 43 days later, on June 2, 1942 the pilot GMC DUKW was run. The DUKW designation came from the General Motors model designation. During the time period in question, the model designations were established by an informal committee consisting of C.J. Bock, Truck Division Engineer; George Oliver, Truck Sales Engineering; and R.A. Crist, production control manager. The model designation convention used by Yellow Truck and Coach consisted of groups of letters and numbers. The first letter in the group represents the year of the vehicle introduction, A being 1939, B being 1940, etc. The second letter is indicative of the type of vehicle – C being conventional, F being Cab over engine, etc. The letter “U” represents “utility,” as it had been previously used to indicate “public utility.” The third and fourth letters represent various special chassis. “K” represents front-wheel drive, while “W” is indicative of 6-wheel dual-driving axles (as with the standard army CCKW 6x6).
The day after the first run of the DUKW, water testing began at Crystal Lake, Michigan. Eleven days later, the Army called and advised that the tests in Virginia were scheduled to begin on Tuesday the 16th. To meet this schedule the team set out for Washington, leaving Pontiac at noon on Sunday, and arriving without incident in Washington at 6 p.m. Monday following an overnight stay in Pittsburg.
The demonstrations began the next day at nearby Fort Belvoir, just as scheduled, with the DUKW carrying 6,000 lbs. in and out of the water, up steep embankments and over moderate land courses. The successful demonstration served to fuel the desire for a surf test. Until such tests could be scheduled, the DUKW would continue testing at Fort Belvoir.
At 3 p.m. on Sunday the 21st, Rod Stephens and the DUKW left Fort Belvoir for Virginia Beach with the temperature near 100 degrees in the shade. The DUKW, with Stephens at the wheel, arrived at Virginia Beach at 11 p.m.
Testing began at Fort Story the next morning. Choppy water conditions proved to be no obstacle at all for the DUKW, although on the beach the DUKW’s movement was very slow in soft sand, and it even became mired in gravel along the edge of the beach while carrying an 8,000-lbs. cargo. These events pointed to the need for improved tires, an additional shovel in the on-vehicle equipment, and some form of a sand anchor, which would permit the DUKW to recover itself absent trees, other vehicles or large rocks to winch against. Further testing indicated that airing the tires down to about 15 lbs. (vs. their 45-pound norm) made a dramatic improvement on the performance in sand. The observers of the tests were very impressed when the DUKW took to the sea with 75 troops aboard.
Tuesday morning, the 23rd, found the waters off Fort Story to be dead calm, disappointing everyone who wanted to subject the DUKW to a more rigorous test. Faced with the disappointing surf at Fort Story, the DUKW team then drove the vehicle, laden with a 3,000-lbs. cargo, and fitted with dual front wheels, the 150 miles south to Kitty Hawk, N.C., in hopes of finding more challenging seas. The team found the seas there no more challenging than those in Virginia, but drove to the Bodie Island Coast Guard Station, where they lowered the tire pressure to 15 lbs. and demonstrated the DUKW for the Coast Guard personnel present. A handful of men, including Rod Stephens and some photographers, opted to keep the DUKW at Kitty Hawk overnight, and the next morning awoke to a hard breeze and very rough surf. The hasty decision to go south from Fort Story the day prior had resulted in the DUKW’s custom fitted cargo and cab covers having been left at the Virginia installation. An expedient cover for the cargo area was rigged, and the DUKW was taken into the boiling sea.
Entering the ocean, the pilot DUKW’s poor left turn ability resurfaced, causing the bow to swing to the right until the truck/boat was broadside to the crashing waves. The sea entered the cab and engine compartment, wetting the engine’s ignition system, causing the engine, which not only drove the vehicle but also the bilge pumps, to stall – and resist efforts to restart. The pounding waves drove the hapless DUKW and her crew broadside onto the beach. All of this was dramatically and dutifully captured on film by the assigned photographers. While this failure dramatically demonstrated the need for a water-shielded ignition system and improved engine compartment sealing, it no less dramatically demonstrated the rough water ability and stability of the basic hull design – attributes that later would save the lives of thousands of men.
Once the vehicle came to rest, the crew dried the ignition and restarted the engine – only to find that the vehicle, still burdened with its 3,000 lbs. of cargo, could not negotiate the sand crest without the use of the winch. Rod Stephens, in his report on this event, stated that this pointed to the need for:
(A) Sand Anchor
(B) Better Tires for Sand
(C) More power and speed on beach
All of these attributes would be found in time in the production vehicles.
Following the experiences at Kitty Hawk, the Army immediately ordered the DUKW driven back to Pontiac for modification, and for use as a guide in the production of four additional pilot models.
Based on the tests conducted up to that point, Sparkman & Stephens revised the hull design.
A method for shielding the ignition shielding was worked out, thereby not only solving the drowned ignition issue experienced at Kitty Hawk, but also providing radio suppression for the engine.
With the design improved, fabrication of four additional pilots was completed, followed by initiation of series production.
With production of the DUKW under way in Pontiac, training of DUKW crews got under way at Camp Edwards on Cape Cod. On Nov. 10, 1942 pilots 1 and 4 and a detachment of Camp Edwards’ Engineer Amphibian Command under Captain Friberg were dispatched from Camp Edwards at the southwestern base of Cape Cod Hook, 70 miles away to Provincetown, Mass., located on the inner shore near the extreme northern end of the Cape.
Gradually, over the next six days, seas up to 6 feet on the Atlantic side of Cape Cod Hook tested the surf ability of the DUKWs and their crews.
On Nov. 25, the first four production DUKWs reached Provincetown, joining the pilot vehicles already there, bringing the roster of the detachment of Camp Edwards’ Engineer Amphibian Command under Captain Friberg to eight vehicles.
Rescue of the crew of the Rose
Shortly after midnight the morning of Dec. 2, 1942 one of the most oft repeated stories concerning the development of the DUKW began to unfold off Cape Cod. A Coast Guard Auxiliary, a yawl about 50-feet on the water line, which was on lookout for U-Boats, had gone aground off Highland Light. The winds were blowing 40 to 60 mph, driving a hard rain and stirring up high waves. The crew of the vessel, which before military service had been known as the Rose, radioed Boston advising she was aground, but the crew was unharmed. Sea conditions, however, were such that the crew could not reach shore either by swimming or by means of lifeboat or raft. Coast Guard personnel from three stations had been dispatched, with breeches buoy gear as well as a surfboat. Upon their arrival, it was learned that the shoreline was too low to permit the use of the breeches buoy, and that the wind and current made use of the surfboat inadvisable.
Commander Allison of the Coast Guard placed a call to the Towne House, the beachfront hotel in Provincetown which was serving as quarters for the Provincetown detachment of the Engineer Amphibian Command. Responding to this call, around 1 a.m. Rod Stephens, Palmer C. Putnam, and Roger Warner, Jr., along with Commander Allison and fortuitously accompanied by noted maritime photographer Stanley Rosenfeld, left the Towne House with two DUKWs bound for the beach about one mile from Highland Light. Upon reaching the sand, tire pressure was reduced to 8 lbs. The DUKW men briefly conferred with the Coast Guardsmen on the beach, who told them that if they wanted to “try” to rescue the seven-man crew of the yawl, they were welcome to. It was decided that one DUKW, manned by Rod Stephens, Palmer C. Putnam, Commander Allison, and his Chief Silva would attempt the rescue. The other DUKW and crew would remain on shore unless summoned by the rescue crew.
Rod Stephens would later describe the rescue trip as “extremely uneventful,” with the Rose’s crew and their belongings returning to shore in less than six minutes. Back on land, discussions with Rose’s skipper indicated it would be advisable to run out an anchor from the vessel into deep water. Stephens, Putnam, and Chief Silva, together with the skipper of the Rose, and a member of her crew, and accompanied by the photographer Rosenfeld, returned to the vessel and laid out the anchor.
In his biography All of This and Sailing Too, Olin J. Stephens II wrote: “Stanley was well equipped and brought back some pretty dramatic nighttime pictures of the rescue.” These photos, now seemingly lost in the vast expanse of government archives, would play an important role in the future of the DUKW. Copies of these photos were immediately supplied to NDRC head Vannevar Bush, who took them to Secretary of War Henry L. Stimson, and told him the story of the rescue. Bush picked up the story of the photos and the rescue account in his book Pieces of the Action: “Mr. Stimson took them to a Cabinet meeting and waited until Mr. Knox [Secretary of the Navy Frank Knox] was close by, and then told the President that this was probably the first case in history in which a naval vessel had been rescued by an Army truck. This eased off some of the opposition.”
As for the Rose, when the DUKWs and the crew of the Rose returned at 6:30 a.m., no trace of the vessel could be found.
Throughout WWII and the Korean War, the DUKW served competently in sometime extreme weather. The vehicles were operated by trained crews, well maintained, and equipped with their original powertrain, including waterproof ignitions. Their power-operated bilge pumps were backed up by manually operated pumps that were carried as on vehicle equipment.
The DUKW, as designed by the NDRC team and produced by General Motors, proved itself to be unquestionably the most successful amphibious vehicle used by the U.S. – or any other military – to date. J
Excerpted from the author’s “The Complete DUKW Historical Reference”, ISBN 978-0-89747-720-8, available from DavidDoyleBooks.com.
Scan the QR code below with your smart phone to watch a video of a successful launch, swim and recovery of Steve Greenberg’s restored GMC DUKW.
*As an Amazon Associate, Military Trader / Military Vehicles earns from qualifying purchases.
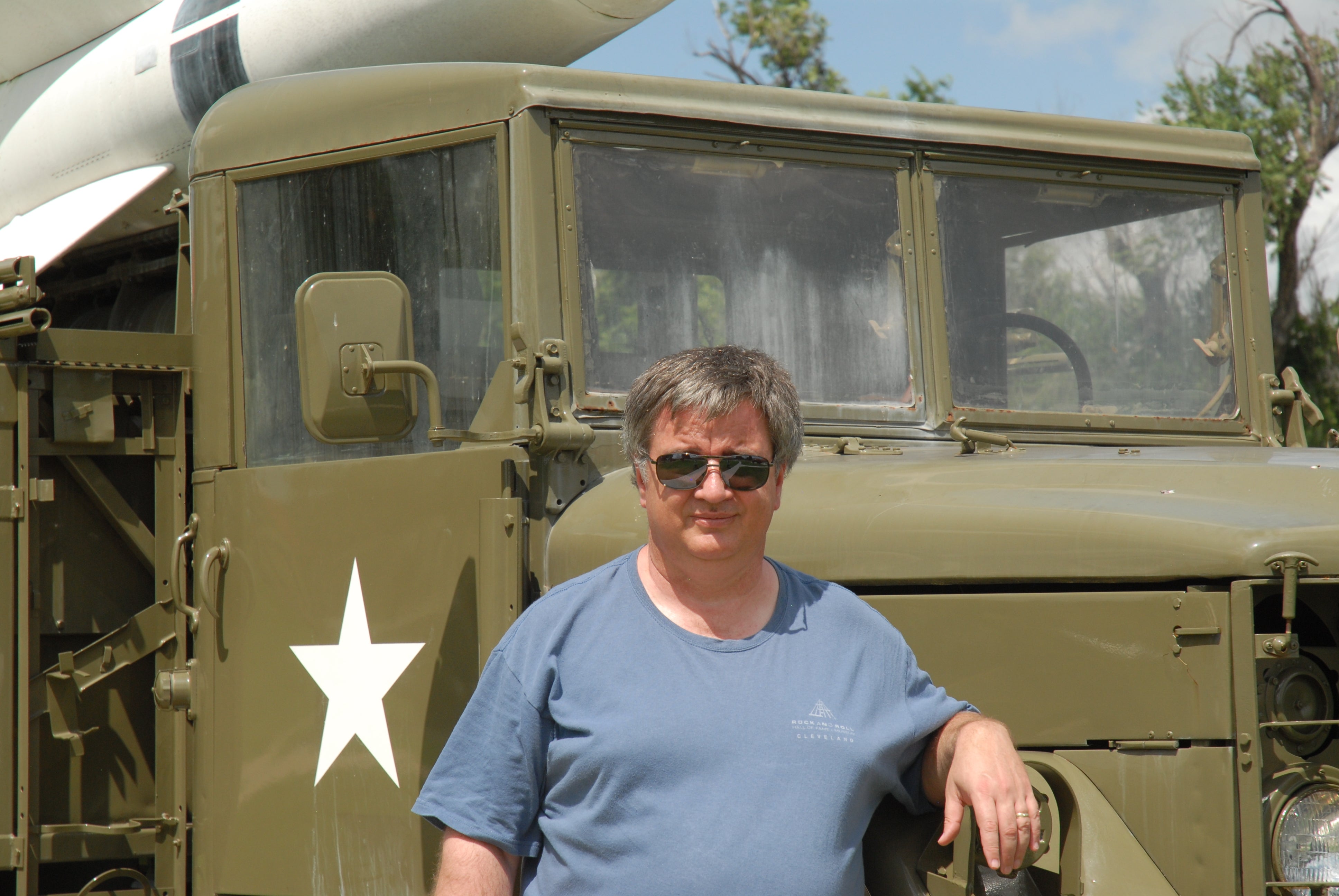
David Doyle's earliest published works were occasional articles in enthusiast publications aimed at the historic military vehicle restoration hobby. This was a natural outlet for a guy whose collection includes several Vietnam-era vehicles such as M62, M123A1C, M35A2, M36A2C, M292A2, M756, and an M764.
By 1999, his writing efforts grew to include regular features in leading periodicals devoted to the hobby both domestically and internationally, appearing regularly in US, English and Polish publications.
In 2003, David received his a commission to write his first book, The Standard Catalog of U.S. Military Vehicles. Since then, several outlets have published more than 100 of his works. While most of these concern historic military hardware, including aircraft and warships, his volumes on military vehicles, meticulously researched by David and his wife Denise, remain the genre for which he is most recognized. This recognition earned life-time achievement in June 2015, when he was presented Military Vehicle Preservation Association (MVPA) bestowed on him the coveted Bart Vanderveen Award in recognition of “...the individual who has contributed the most to the historic preservation of military vehicles worldwide.”
In addition to all of publishing efforts, David is the editor of the MVPA’s magazine, History in Motion, as well as serving as the organization’s Publications Director. He also maintains a retail outlet for his books online and at shows around the U.S.